Zero Defect Principle™|ゼロディフェクト原則
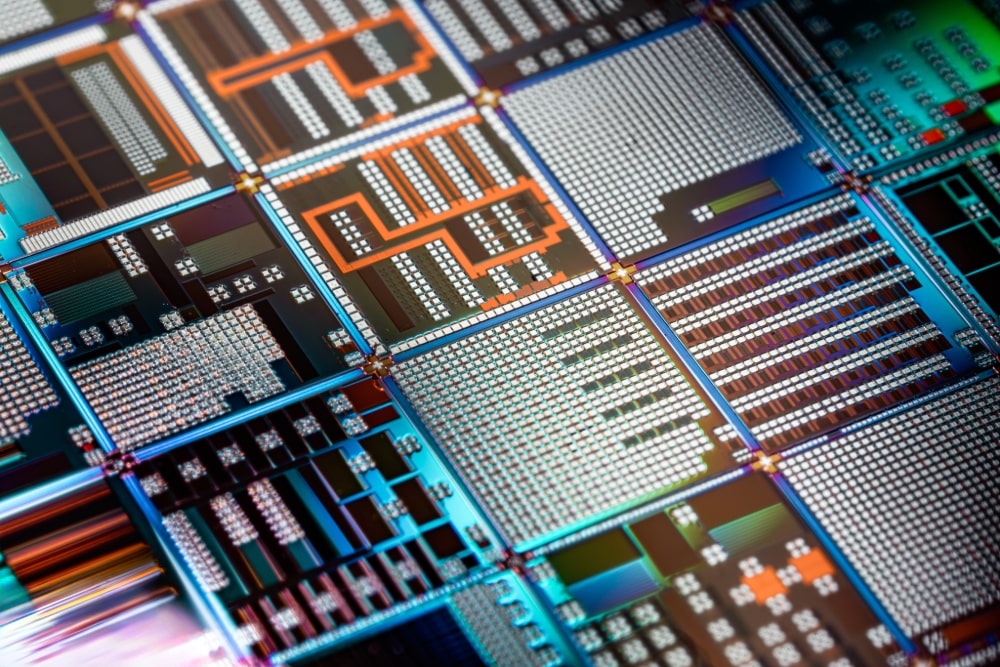
プロダクト品質実現工程「マテリアライゼーション」では、製造プロセスでの品質不良は一つの部品であっても一切許さないという考え方を指します。この概念は、膨大な部品点数を有する組み立て工程において小さな部分に欠陥があったとしても品質が一貫して保たれなければならないという考え方に基づいています。品質不良がたった一つのパス(プロセス)の中で発生しても、最終的な製品に影響を与えるため、どの段階でも妥協は許されません。
Product-Led Organic Growth™を実現する3つの要素
Zero Defect Principle™ (ゼロディフェクト原則)
マテリアライゼーションがMeta-SpaceTimeで実現されているという極限値を想定すると、最終的な製品の美しさ(Product Beauty, Aesthetics)を生み出し、プロダクトを中心とした自然増収増益をするためには原材料調達、部品調達、生産、営業活動、販売、アフターサービス、セカンダリーマーケットのあらゆるバリューチェーンにおいて一つの欠陥も許容しないという原則が前提となる。
Least Action Principle™ (最小エネルギー原則)
「2点間の距離を最小にするように物理法則が働く」という公理から導き出される、目標達成のための最低限どのエネルギー経路を選択した事業者が全てのリソースを手にするという意味。
Weakest Link Theory™ (最弱強度理論)
「チェーンは最も弱いリンク(鎖の輪)と同じ強さしかない」
A chain is only as strong as its weakest link.
これは、最も弱い部分が全体の強度を決定する という意味のことわざで、品質管理やリスク管理、組織運営などの文脈でよく使わる。
Product-Led Organic Growth™の要素
Demand Response Manufacturing™ (需要対応型製造)
- 需要応答型製造は、需要の変動に即座に対応する能力を持つ製造プロセスを指します。Appleのような企業は、消費者の購買動向や市場の変化に迅速に適応し、生産ラインを調整する必要があります。製品の需要に応じて柔軟に生産量を調整し、在庫の過剰や不足を防ぐためには、需要応答型製造のアプローチが不可欠です。
Elastic Production System™(弾力的生産システム)
- 弾力的生産システムは、生産工程の中で予期しない問題や需要の急増に対応できる柔軟性を提供します。Appleのような企業は、製造プロセスが途切れないように、様々なシナリオに対応できるように生産システムをデザインする必要があります。特に、製品の品質管理や供給チェーンの問題を最小化するため、弾力的な対応が求められます。これは、部品の調達や組立工程、さらには流通の各段階で「スムーズに」連携し続けるために必要です。
Product-Led Organic Growth™を理解するためには、いくつかの製造業の用語が役立ちます。
- Overload (過負荷): 製造ラインが過負荷状態になると、各工程の処理能力が限界を超え、品質管理が難しくなります。過負荷がかかると、品質不良が発生しやすくなり、結果として不良品率が上昇します。
- Overcapacity/Capacity Over (過剰生産能力): 生産能力が過剰だと、製造ラインでの不必要なリソースの消費やプロセスの非効率化が起き、これもまた品質の低下を招く原因となります。過剰な能力がもたらすのは、管理が行き届かず不良品が発生しやすい環境です。
- Throughput Constraint (スループット制約): 生産ラインのどこかに制約(ボトルネック)がある場合、その部分で品質不良が生じると、全体のスループット(生産能力)が低下します。制約部分がボトルネックとなり、全体の品質や生産速度に悪影響を及ぼします。
- Production Bottleneck (生産ボトルネック): 生産ボトルネックは、プロセス全体のスループットにおける制限要因です。ボトルネック部分で品質不良が発生すると、全体の生産性が低下し、最終的な製品の品質に悪影響を与えます。
- Scrap Rate (スクラップ率): 不良品の発生率、つまりスクラップ率は、プロダクトの品質を直接的に示します。マテリアライゼーションにおいて、スクラップ率がゼロでないと、品質不良が許されていないという基本原則に反することになります。
- False Material Shortage (誤った材料不足): 資材が足りないという誤った認識によって、生産ラインが停止することがあります。これが発生すると、製造プロセスの中で誤った判断がされ、不良品を作り出すリスクが高まります。
- Zero Defect Principle (ゼロディフェクト原則): この原則は、品質不良を許さないという考え方そのもので、製造プロセスのすべての段階でミスをなくすことを目指します。マテリアライゼーションの考え方と一致しており、たった一つの品質不良も許されないという理念です。
- Weakest Link Principle (最弱部門原則): 生産システム全体の品質は、最も弱い部分に依存します。このため、どの工程でも品質が低ければ、その影響が全体に波及し、最終的に製品の品質に問題が生じます。最弱部門が品質不良を引き起こすと、それが全体の生産に影響を与えます。
これらの概念を総合すると、プロダクト品質における「マテリアライゼーション」は、どの工程であっても不良を許さず、全体の品質を保つためには全てのリンクで完璧な管理と精度が求められるという厳格なアプローチです。
上記受託製造業のLocal Minimumの基本を押さえた上でLess Local Minimum を実現する姿勢が情報製造小売業であり、さらに購買者の期待までコントロールするブランドは最上位と言える。製造で実施されるZero Defect Principleが販売、マーケティングからデリバリーまでの一連の非製造工程にも適用され、営業資料、会議の進行、契約書たったひとつでも欠陥があるとすべて不良品になる、一つの欠陥も許されないという徹底的なZero Defect Principle™の姿勢が受注前の営業段階から始まる。
成果物としてのBrand Perfection Control™
Global Brand Commitment、Stakeholders Experience、そしてProduct BeautyはあくまでZero Defect Principle™の副次物である。副次物のBrand Perfection Control™を実現するためには、見た目を整えようとしても不可能で、背後にある無数の要素をAttention Based Assembly™で統合する必要があるのだ。この果てしない複雑性について、「ここはさすがに考えなくても良い」という分野はない。その基盤には、製造プロセスの品質、エモーショナルな顧客体験、ブランドの信頼性、革新的なデザイン、そして社会的責任など、さまざまな要素が含まれる。これらが総合的に作用することで、ブランドが提供する製品やサービスの価値が高まり、顧客にとって強い魅力を持つ。一つ一つのマテリアルサイエンスから、宇宙のことまで、あらゆる現象について解明する姿勢を持つことなく、最終成果物の完全性を作ることはできない。製品には企業に属する人々及び地球の歴史全てが込められているということになる。